Food packaging plays a primary role in our convenience-oriented society. Pre-packaged meat and produce, fast food and take-out container manufacturing contribute greatly to the use of plastics that will ultimately be thrown away. Packaging technology must therefore balance convenience with food protection, energy and material costs, heightened social and environmental consciousness, and strict regulations on pollutants and disposal of municipal solid waste.
As a chemical foaming agent, Safoam™ contributes to environmental responsibility by providing a means to food packaging manufacturers to reduce polymer use, energy and overall costs. As a nucleating agent, Safoam™ has allowed significant reductions in the use of Hydrofluorocarbons (HFC), which have a high Global Warming Potential (GWP). Safoam™ products used in these applications are G.R.A.S. (generally recognized as safe) by the FDA for direct food contact.
Learn More
There are various plastic sheets with many variances of thicknesses produced. Sheets and boards are made with many type of resins including PP, PE, PVC, PC, EVA, and many others. Depending on the structure being produced, some sheets are then thermoformed into a structure.
Safoam™ can help remove weight from the overall sheet to allow for up to 30% weight reduction, improved through put, and provide overall cost savings. Safoam™ can also act\ as a nucleator in a direct gas system by producing a fine, uniform cellular structure. If VOC’s are a concern, the gases evolved with Safoam™ will allow for reduced usage of the physical gas used.
Learn More
Fossil fuel pipelines are expected to be a safe and efficient means of energy transportation. Originating in wells in various supply regions around the world, these fuels will travel thousands of miles to their destination markets. Impurities are removed at treatment plants, and from there, usable product flows through the mainline, compressed at intervals along the way to propel it forward. Finally, the oil or gas is transported to local distribution companies that deliver them to customers in various industries and homes.
Transporting this precious commodity requires pipeline that is dependable. One of the world's largest manufacturers of subsea oil and gas transmission pipelines depends on Safoam™ products to give consistent and beneficial results. Aside from weight reduction and faster throughput, this company has found that they reliably achieve uniform foamed thermal insulation, and meet precise density, compressive creep resistance and thermal conductivity criteria.
Learn More
In 2012, NHTSA established final passenger car and light truck CAFÉ standards for model years 2017-2021, which the agency projects will require in model year 2021, on average, a combined fleet-wide fuel economy of 40.3-41.0 mpg. As part of the same action, EPA issued GHG standards, which are harmonized with NHTSA’s fuel economy standards that are projected to require 163 grams/mile of carbon dioxide in model year 2025. Numerous methods will contribute to meeting these goals. Reducing vehicle weight will be the primary method, and Safoam™ will continue to play a role. Parts large and small - brackets, instrument panels, doors, overheads - the entire auto body - are candidates for foamed thermoplastics.
Light-weighting is one benefit of foaming. A molded component with a closed, evenly-dispersed microcellular structure allows for parts with better dimensional stability, faster cycle times and sound-deadening. Extruded body side molding and thermoformed panels can see similar benefits.
Learn More
Plastic building materials have seen tremendous and continual growth in the building and construction industry. Above all, professionals find plastic building materials easy to maintain. More and more designers and owners prefer plastic building materials because they require little to no maintenance, and can withstand heavy use and harsh elements.
Plastic building products are affordable, durable, and safe. As better quality plastic building products with more design appeal have become available, new materials are offering an array of design solutions. Safoam™ is currently utilized in such applications as window profiles, trim molding, siding and decking. Straighter profiles, increased load-bearing strength and improved insulation accompany lighter weights and faster throughput. Safoam™ has also been used as a special effect colorant for faux wood, as an alternative to lamination.
Learn More
Think about all the things you touch throughout the day that are made of plastic. Toothbrushes, containers, broom handles and blocks, toys and play equipment are all made of plastic. Years ago, many of these items would have been made of glass, wood or metal. Due to energy efficiency, durability and design flexibility, plastic has become the product of choice in manufacturing so many of the items we use every day.
The addition of Safoam™ to the manufacturing process reduces cost by allowing a 25% improvement in production time while providing lighter, stiffer parts without compromising the part's integrity.
Learn More
Safoam™'s microcellular structure adds to the flexibility and protective properties without compromising signal strength when foaming wire and cable. There are significant insulation properties resulted through a fine, uniform cellular structure.
Learn More
Plastic conduit is a tube used to protect and route electrical wiring and cables in a building or structure. Conduit can be made with PVC, TPU, polyolefins, polyamide, and other resins. Electrical conduit provides very good protection to enclosed conductors from impact, chemical vapors, and moisture. Some types of conduit systems are approved for direct encasements in concrete. Conduit systems are generally classified by their mechanical stiffness, wall thickness, and resin used to make the tubing.
Safoam™ benefits are often applied when foaming conduit to help remove sink marks and defects on the part as well as prevent warpage. It can also provide uniform cell structures throughout the part allowing for better insulation properties.
Learn More
Commonly used items such as appliances are a very growing and evolving market. Household appliances can be classified into three major categories such as white goods, small appliances, and consumer electronics. Major appliances are large home appliances used for regular housekeeping tasks such as cooking, washing laundry, food preservation, and others.
The appliance industry can benefit from Safoam™'s ability to reduce a significant amount of weight on mechanical parts while retaining strength and functionality. Thermoformed refrigerator interiors can achieve lighter weights while improving thermal insulation. Dishwashers with foamed interiors can see similar benefits while also improving sound deadening. Often parts can be molded and foamed to allow for improved cycle times and machine energy savings.
Learn More
Plastic garden furniture is the perfect choice if you are looking for something to leave outside all year long. Lightweight, durable and weather-proof, a quick wipe-down and it's ready for use. Design flexibility and unlimited color choices make plastic garden furniture ideal for rigid profiles like park benches, decking & railing; flexible extrusions like garden hose and fatigue mats; injection molded post caps, tables, chairs and loungers, and so much more.
Lighter weights, straighter profiles and improved load bearing are hallmarks of Safoam™'s contributions. Additives for improved performance in Wood-Plastic composites allow higher wood content and lighter weight. Several Safoam™ products can be used as a compatibilizer for recycled resins, furthering our commitment to environmental responsibility.
Learn More
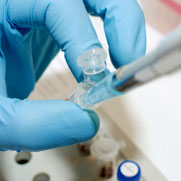
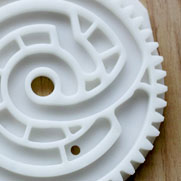
The medical devices market has evolved with respect to the types of devices produced, substrates selected, and sterilization procedures utilized. In the early 1970s, manufacturers were using glass, rubber, and metal to assemble syringes, surgical instruments, and other devices. Products made from such materials were typically machined, molded, or assembled with fasteners. The 1980s saw expanded use of engineering plastics. These materials became indispensable for use in intricate, high-performance device designs. A shift to single-use devices caused design engineers to consider polymers like acrylic, polycarbonate, and PVC.
Advances in high performance polymers and the associated merits of plastics over other materials have expanded the opportunities of plastics in the medical industry, not only in devices but also in packaging. Price pressures in the healthcare industry are also driving the development of high-quality, low cost alternative polymers. Approved for food contact by the FDA, Safoam™ has been used in diagnostic equipment and jackets for surgical tubing.
Learn More